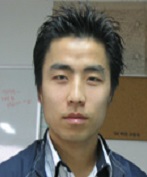 |
Kim, Hyung Won (김형원)
Email:
Research Area:
Occupation: LG-Display
2008 M.S. Graduation Thesis:
Scheduling Algorithms for Hybrid Flow Shops with Reentrant Flows and Unrelated Parallel Machines
This thesis considers the scheduling problem in reentrant hybrid flow shops with parallel machines at each serial production stage. In reentrant hybrid flow shops, each job may visit each production stage several times, called the reentrant product flows in the literature. As an extension of the existing research, we consider the unrelated parallel machines at each stage and hence the processing times of a job depends on the machine where the job is processed. The problem is to determine the allocation of jobs to unrelated parallel machines as well as the sequence of the jobs assigned to each machine for the objectives of minimizing makespan and total tardiness. Since due-dates must be satisfied after negotiated with customers in most practical situations, the problem is transformed into the one with a single objective of minimizing makespan by moving the tardiness objective to a constraint set with a certain allowance. Due to the complexity of the problem, two heuristics are suggested and tested in this thesis. In particular, the two heuristics are competitive to a search heuristic with sufficiently long computation time.
2018 Ph.D. Graduation Thesis:
Deterministic and Stochastic Models for Selective Disassembly Sequencing with Sequence-dependent Setups in Parallel Disassembly Environment
This dissertation focuses on the selective disassembly sequencing problem with sequence-dependent setups in the parallel disassembly that removes one or more components at the same time by a single disassembly operation. The problem is to determine the sequence of disassembly operations to extract multiple target components while satisfying the precedence relations among disassembly operations. In this dissertation, we consider one deterministic model and two stochastic models for the selective disassembly sequencing problem. In Chapter 2, we suggest the deterministic model for the selective disassembly sequencing problem. The problem is to determine the sequence of disassembly operations to extract multiple target components while satisfying the precedence relations among disassembly operations. The objective is to minimize the sum of sequence-dependent setup and operation costs. An integer programming model is developed after representing all possible disassembly sequences using an extended process graph, and then an optimal branch and bound algorithm is proposed that incorporates the methods to obtain the lower and upper bounds as well as a dominance property to reduce the search space. To show the performance of the algorithm, computational experiments are done on various random vi instances, and the results are reported. In particular, it is shown from the test results that the proposed algorithm requires much shorter computation times than a competitive commercial software package. Finally, a case is reported to illustrate the extended process graph and the solution algorithm. In Chapter 3, we propose two stochastic models for the selective disassembly sequencing problem. The first one is the problem that considers random operation times in the parallel disassembly environment in which one or more components can be removed at the same time by a single disassembly operation. An extension of the first one, the second one is the problem that considers irregular disassembly operations and random operation times. Here, the irregular operations are defined as those in which fasteners can be removed by additional destructive operations without damaging to the target components. After representing all possible sequences using the extended process graph, two stochastic integer programming models are developed that minimizes the sum of disassembly and penalty costs, where the disassembly cost consists of sequence-dependent setup and operation costs and the penalty cost is the expectation of the costs incurred when the total disassembly time exceeds a given threshold value. A sample average approximation algorithm is proposed that incorporates an optimal algorithm to solve the sample average approximating problem under a given set of scenarios for each problem. The algorithm is illustrated with a hand-light case and a large sized random instance, and the results are reported.
Lab Seminars:
1. |
Selective disassembly planning for the end-of-life product.  |
2017.08.08 |
2. |
Probability Evaluation Modeling and Planning of Product Disassembly Profit  |
2017.01.24 |
3. |
A Chance Constrained Programming Approach to Determine the Optimal Disassembly Sequence  |
2016.08.09 |
4. |
Probability evaluation models of product disassembly cost subject to random removal time and different removal labor cost  |
2016.07.20 |
5. |
Integrated multi-layer representation and ant colony search for product selective disassembly planning.  |
2016.02.04 |
6. |
Disassembly sequence structure graphs: An optimal approach for multiple-target selective disassembly sequence planning.  |
2016.01.12 |
7. |
Evolutionary sequence planning for selective disassembly in de-manufacturing.  |
2015.01.13 |
8. |
Scheduling jobs under constant period-by-period resource availability to maxmize project profit at a due date.  |
2011.01.04 |
9. |
Scheduling jobs under constant period-by-period resource availablility to maximize project profit at a due date IJAMT |
2010.2.08 |
10. |
Network decomposition techniques for resource constrained project scheduling JORS |
2010.2.08 |
11. |
Scheduling a project to maximize its net present value - An integer programming approach EJOR. |
2010.1.18 |
12. |
Economic lot-sizing with remanufacturing options. (7.06) |
2010 |
13. |
Inventory optimization in a one product recoverable manufacturing system. (7.27) |
2010 |
14. |
Heuristic for Multistage Production Planning Problems. (8.24) |
2010 |
15. |
The multiple resource constrained project scheduling problem : A breadth-first approach. (1.14) |
2009 |
16. |
R&D project selection and scheduling with a filterd beam search approach. (2.08) |
2009 |
17. |
Multiple resource constrained scheduling using branch-and-bound. (3.04) |
2009 |
18. |
Project selection, scheduling and resource allocation with time dependent returns. (7.15) |
2009 |
19. |
. Analysis of scheduling schemes and heuristic rules performance in resource-constrained multi-project scheduling. (8.05) |
2009 |
20. |
A branch-and-bound procedure for the multiple resource-constrained project scheduling problem. (8.25) |
2009 |
21. |
Work force size and single shift schedules with variable demands(2.3) |
2008 |
22. |
A multiple shift workforce scheduling model under annualized hours(2.26) |
2008 |
23. |
Multiple shift workforce scheduling under the 3-4 workweek with different weekday and weekend labor requirements(1.13) |
2008 |
24. |
Branch and bound algorithms for the multi-product assembly line balancing problem (08.06) |
2008 |
25. |
Branch and bound algorithms for simple assembly line balancing problem (07.23) |
2008 |
26. |
Simulated annealing heuristic for flow shop scheduling problems with unrelated parallel machines (2.22) |
2007 |
27. |
Minimizing makespan on an m-machine re-entrant flowshop (2.1) |
2007 |
28. |
A heuristic for scheduling a permutation flowshop with makespan objective subjective to maximum tardiness (1.11) |
2007 |
|