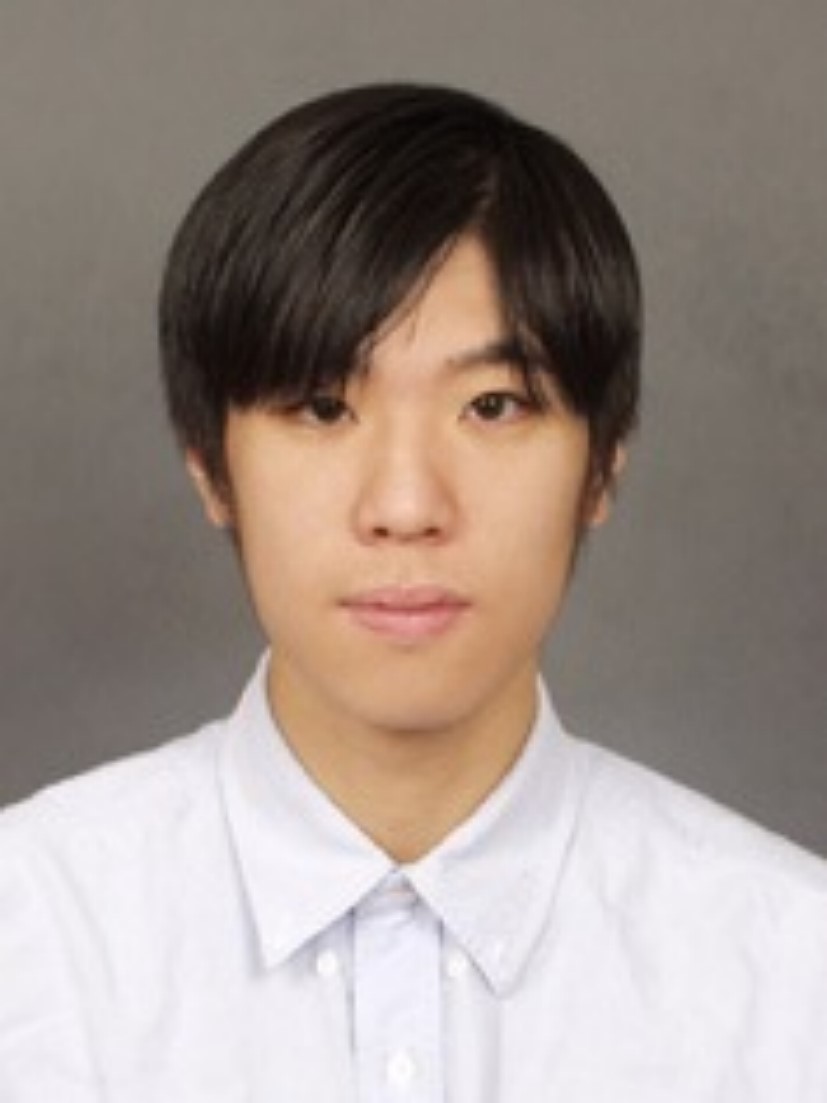 |
Yu, Jae Min (유재민)
Email:
Research Area:
Occupation: Hanyang University
2009 M.S. Graduation Thesis:
Scheduling Algorithms for Job Shops with Job Families: Minimizing the Sum of the Maximum Family Flow Times
This paper addresses the scheduling problem for job shops in which jobs are grouped into job families for further assembly operations, but processed individually. The job shops considered in this paper can be found in various production systems, especially in remanufacturing shops that process parts or components obtained after disassembling used or end-of-life products. The main decision is the sequence of the jobs assigned to each machine, which is the same as that of the ordinary job shop scheduling problem. To minimize the deviations of the job completion times within each job family, the objective is set to minimizing the sum of the maximum family flow times. To describe the problem mathematically, an integer programming model is presented. Then, we suggest 2-phase methods: (a) obtaining initial solutions using priority rules based heuristics, (b) neighborhood generation methods for improvement Computational experiments were performed on various test problems and the results are reported.
2018 Ph.D. Graduation Thesis:
Due-date based Scheduling Algorithms for Job-shop-type Remanufacturing Systems with Component Matching Requirement
This dissertation focuses on a scheduling problem for remanufacturing systems with parallel disassembly workstations, a job-shop-type reprocessing shop and parallel reassembly workstations, in which the components obtained by disassembling an end-of-use/life product must be matched when reassembling the corresponding remanufactured product, i.e. component matching requirement. In this dissertation, we first consider a scheduling problem for job-shop-type reprocessing shop with component matching requirement. Then, a scheduling problem for job-shop-type reprocessing shop and parallel reassembling workstations is considered. Finally, a scheduling problem for the entire remanufacturing system composed of parallel disassembly workstations, a job-shop-type reprocessing shop and parallel reassembly workstations is considered. In Chapter 2, a job-shop-type reprocessing shop with component matching requirement iv is considered. To consider the component matching requirement, we propose a job shop scheduling problem in which jobs are grouped into job families, but they are processed individually using their distinct routings. Unlike the previous studies, we consider a duedate based objective of minimizing the total family tardiness, i.e. sum of positive deviations between the due-dates and the completion times of job families. A mixed integer programming model is developed to present the problem mathematically. Then, an optimal algorithm is proposed using the branch and bound technique while developing a job family based lower bound. For practical applications even with the large-sized job instances, two types of heuristics, shifting bottleneck based and priority scheduling algorithms, are also proposed. To test the performances of the three types of solution algorithms, computational experiments were done on various test instances and the results were reported. In Chapter 3, we consider a scheduling problem of determining the sequence of the jobs to be processed on each workstation of job-shop-type reprocessing shop and the allocation/sequence of the jobs to be performed on parallel reassembly workstations. To cope with component matching requirement, the reprocessing jobs are grouped into job families corresponding to products to be remanufactured. A mixed integer programming model is proposed for the objective of minimizing the total tardiness. Then, two solution approaches, sequential and integrated ones, are proposed. The intuitive sequential approach solves the reprocessing and the reassembly scheduling sub-problems in sequence while the integrated approach solves them simultaneously after representing the problem as an extended disjunctive graph. It is shown from computational tests that the integrated one outperforms the intuitive sequential one significantly. Also, the absolute performance of the better integrated approach is reported using the gaps from optimal solution values for small sized test instances.
Lab Seminars:
1. |
A simulation analysis of part launching and order collection decision for a flexible manufacturing system  |
2017.08.22 |
2. |
Reentrant FMS scheduling in loop layout with consideration of multi loading-unloading stations and shortcuts  |
2017.02.16 |
3. |
A study on local search neighborhoods for the job shop scheduling problem with total tardiness objective  |
2016.08.02 |
4. |
Evaluation of scatter-search approach for scheduling optimization of flexible manufacturing systems  |
2016.07.14 |
5. |
A branch & bound algorithm for the open-shop problem.  |
2016.02.02 |
6. |
A branch-and-bound algorithm to minimize total weighted completion time on identical parallel machines with job release date.  |
2016.01.07 |
7. |
Tardiness minimization on parallel machines.  |
2015.01.23 |
8. |
Adjustment of heads and tails for the job-shop problem.  |
2012.01.17 |
9. |
An Implicit Enumeration Algorithm for the Machine Sequencing Problem. |
2010.1.27 |
10. |
Machine sequencing via disjunctive graphs: An implicit enumeration algorithm. |
2010.1.12 |
11. |
Job shop scheduling with alternative machines. (7.09) |
2010 |
12. |
Linguistic-based meta-heuristic optimization model for flexible job shop scheduling. (7.26) |
2010 |
13. |
Mathematical models for job-shop scheduling problems with routing and process plan flexibility. (8.17) |
2010 |
14. |
An Algorithm for Solving the Job-Shop Problem. (1.07) |
2009 |
15. |
Computing lower and upper bounds for a large-scale industrial job shop scheduling problem. (1.28) |
2009 |
16. |
A note on single-machine scheduling with decreasing time-dependent job processing times. (2.08) |
2009 |
17. |
Lagrangian bounds for just-in-time job-shop scheduling (07.23) |
2008 |
18. |
A fast taboo search algorithm for the jop shop problem (08.13) |
2008 |
19. |
Minimizing production flow time in a process and assembly job shop (08.26) |
2008 |
20. |
Simple priority rule combinations: an approach to improve both flow time and tardiness (8.21) |
2007 |
21. |
Performace of static priority rules for shared facilities in a remanufacturing shop with disassembly and reassembly (8.7) |
2007 |
22. |
Stochastic Scheduling with Release Dates and Due Dates (7.24) |
2007 |
|